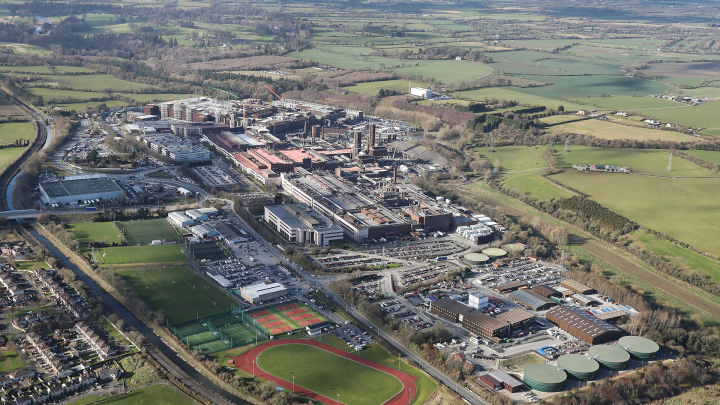
- Major multinational semiconductor manufacturer
- Leixlip, Co Kildare
- Exyte, Jacobs
- 1989 to present day
Continuity and consistency in a complex environment
Across more than thirty years, BAM has delivered numerous projects on this dynamic high-tech campus in rural County Kildare.
BAM has been working on this advanced semiconductor manufacturing campus since 1989, delivering a wide range of specialist civil, structural and architectural works.
Our multinational client has invested billions in growing and developing the 360-acre site. The changing demands and stringent requirements in this ever-evolving industry mean that every aspect of the work undertaken by BAM is painstaking, complex and subject to extremely fine tolerances.
It’s a testament to the trust that has built up between BAM and client – working through a number of project management companies over the decades – that the relationship has endured and become stronger.
Towards the end of the 1980s, one of the world’s leading microchip manufacturing companies chose a former stud farm at Leixlip in County Kildare as the location for its European manufacturing facility. Since then, the site has become home to one of Europe’s biggest on-going construction projects.
In March 2022, the company unveiled the largest pan-European investment programme in its history, including significant investment plans for its Irish facilities, aimed at building a next-generation semiconductor ecosystem in Europe.
BAM has been successfully working on this huge, high-tech campus since 1989: from enabling works to full design and build projects, right through to decommissioning and de-installation packages.
Delivering the cleanroom
One of BAM’s recent projects is at the heart of the client’s largest and most ambitious development in Ireland, with the construction and fit-out of a huge semiconductor fabrication (fab) building, including a technically advanced cleanroom space.
Producing semiconductor chips involves using highly sensitive materials to create delicate layers that must be worked with great care. Not just manufacturing, but also testing and packaging have to be carried out in a carefully controlled environment to eliminate all dust. Cleanrooms in this industry are typically cleaner than a hospital operating theatre.
Work on the new fab began with the excavation and removal of over one and half million cubic metres of soil and stone. The spoil was transferred to a disused quarry nearby, where it is being reclaimed for land use.
BAM then installed 1,400 reinforced concrete piles to create the secant pile wall around the perimeter of the site, designed to protect existing structures on site during construction.
The fab building at the heart of the new development used 150,000 cubic metres of structural concrete and 25,000 tonnes of reinforcements, in the form of over a thousand precast concrete columns and 1,300 precast wall segments.
Finally, BAM undertook the fit-out of the extensive class 1000/100 cleanroom space, to facilitate nanoscale manufacturing to ISO 15644 protocol level 5/6.
Building relationships
Over three decades and more, BAM has become well attuned to working on this highly complex and dynamic site.
It’s not just a question of meeting tight deadlines, but also working alongside other contractors, as well as numerous M&E and other specialist suppliers.
The construction site also sits alongside to a rural community: so it’s vital to ensure that work causes minimal disruption to their everyday lives and takes sensitive account of their concerns
BAM’s experience illustrates how effective communication and close collaboration are key to successful delivery in this fast-moving environment.